Custom Racking Solutions for Heavy Manufacturing: How to Store Oversized and Non-Standard Materials
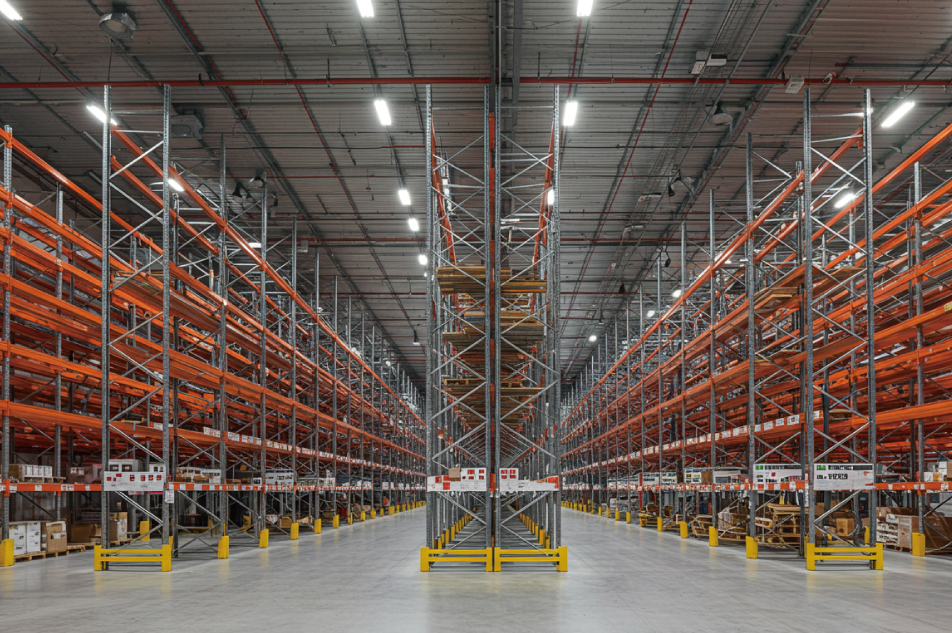
Key Takeaways
- Custom racking solutions resolve inefficiencies tied to oversized and irregular materials.
- Standard racking systems lack structural compatibility for large, awkward, or non-uniform loads.
- Tailored racking designs accommodate shape, weight, and material flow without compromising warehouse safety or accessibility.
- Key challenges include load-bearing limits, floor space consumption, and dynamic inventory rotation.
- Integrating purpose-built racking enhances operational efficiency, reduces damage, and preserves inventory integrity.
Custom Racking in Heavy Manufacturing: An Operational Imperative
Heavy manufacturing environments confront recurring dilemmas when storing long, wide, bulky, or irregular-shaped materials. Items such as steel coils, piping, molds, oversized crates, machine components, and die sets resist uniform handling. Traditional pallet racking systems restrict storage options and exacerbate risks in both retrieval and transport. These materials demand custom-engineered storage infrastructure tailored to the profile, volume, and weight of each load class.
Oversized materials complicate standard warehouse operations, especially where space and accessibility remain limited. Poor racking configurations generate material bottlenecks, lead to retrieval errors, and increase the risk of equipment damage or worker injury. Custom racking alleviates these problems with system architectures designed for dimensional adaptability and structural rigidity.
Why Standard Racking Fails in Non-Standard Scenarios
Most conventional racking systems — selective, drive-in, or push-back — rely on uniform load dimensions. Their design principles assume consistent pallet widths, symmetrical stacking, and predictable weight distribution. When confronted with elongated beams, rounded components, asymmetrical tooling, or non-stackable goods, standard racking becomes incompatible or even hazardous.
Incompatibility Points:
- Load Width: Traditional uprights cannot accommodate items exceeding standard rack widths.
- Load Weight: Structural failure risks increase when storing dense or heavy components without proper support systems.
- Access Paths: Irregular loads compromise forklift clearance and maneuverability.
- Stacking Impossibility: Some units, like turbine blades or custom molds, cannot be stacked safely.
Engineering for Oversized Load Accommodation
The most effective custom racking solutions begin with a detailed load profile assessment. This includes physical dimensions, load distribution patterns, weight range, surface fragility, and material movement frequency. Heavy-duty structural steel frames, adjustable cantilevers, modular decking, and reinforced arms provide foundational flexibility.
Key Design Considerations:
- Weight Distribution: Load weight varies significantly in heavy manufacturing. Each racking solution must stabilize weight without stress concentration.
- Lift Access: Rack design must allow side-loading, overhead lifting, or crane access for extremely large items.
- Dynamic Movement: When loads move frequently, racking needs reinforced anchor points and vibration-resistant elements.
- Custom Decking: Solid decking surfaces such as wire mesh, steel plate, or engineered wood eliminate pressure points for irregular bases.
Heavy-Duty Cantilever Racking: The Default for Long Loads
Cantilever Racking System dominate heavy industries requiring long-load storage. Their open-face design suits pipes, bars, steel beams, and sheet materials. Free of vertical obstructions, cantilever racks support horizontal retrieval without constraining item length. Arms are engineered for heavy weight loads, reinforced with bolt-on bracing to stabilize the frame under dynamic pressure.
Design Parameters for Cantilever Systems:
- Upright height: 2–8 meters, depending on facility ceiling.
- Arm length: customizable to 1500mm+ for beam or pipe lengths.
- Load capacity: up to 5 tonnes per arm for dense material storage.
- Arm types: straight arms for flat goods, inclined arms for cylindrical materials.
Custom Stackable Stillages and Cradles
Stillages and cradles function as modular supports for uniquely shaped loads. Often fabricated from structural tubing with mesh or plate sidewalls, they provide handling stability for castings, drums, or die sets. Custom cradles feature foam linings or contoured bases for component preservation. Unlike fixed racking, they move with the load, allowing rotation without repacking.
Key advantages include:
- Mobility: Stillages double as transport containers, enhancing flow.
- Stackability: Designed to stack safely without weight-bearing concerns.
- Inventory Control: Custom labeling panels and RFID slots assist in tracking irregular SKUs.
Mobile Racking and Adjustable Decking for Flexibility
Some storage environments require periodic reconfiguration. Mobile racking systems address this by mounting racking frames on guided rails. Operators shift entire rows to open aisles on demand. For oversized items that rarely move but consume valuable space, this design allows dense storage without compromising accessibility.
Adjustable decking systems—with slide-in crossbars, pivot arms, or telescoping rails—expand the storage footprint vertically and horizontally. These systems adapt quickly to irregular dimensions, helping manufacturers handle a fluctuating catalog of custom components.
Structural Pallet Racks with Reinforced Beams
While traditional pallet racks falter under extreme weight, modified structural racks with enhanced beams provide a viable alternative. Heavier gauge steel and bolted frame components withstand impact and deflection under persistent stress. Beam profiles—such as C-channel or I-beam—support both static and dynamic storage applications.
Enhancements for Oversized Storage:
- Deep lane configurations for longer loads.
- Crossbars and center supports to avoid deck collapse.
- Fork guides for safe entry and alignment.
- Safety netting or mesh for vertical load containment.
Safety Standards and Compliance for Custom Designs
Custom racking must comply with regional and international standards. AS4084 (Australia), RMI/ANSI MH16.1 (U.S.), and EN 15512 (EU) outline engineering tolerances and loading safety. These codes enforce upright deflection limits, material tolerances, seismic resistance, and safety factors.
Warehouse operators must integrate engineered documentation—load certifications, anchorage plans, and seismic maps—into their compliance workflows. Failure to adhere invites structural failure and legal penalties.
Warehouse Layout Integration
Custom racking cannot be isolated from the broader warehouse layout strategy. It influences aisle width, traffic flow, lift truck paths, and lighting. For oversized loads, wide-span aisles and staging zones are essential. Logistics planners must coordinate racking types with machinery requirements, packaging areas, and outbound docks.
Layout Priorities for Heavy Manufacturing:
Requirement | Design Implication |
---|---|
Oversized Load Width | Expand cross-aisles and storage gaps |
Frequent Retrieval | Position near high-velocity operation zones |
Safety Buffer Zones | Add protective barriers and impact guards |
Forklift Turning | Ensure open radius in all load approach paths |
Benefits Beyond Capacity
The impact of customized racking extends beyond raw storage capacity. Long-term value includes:
- Damage Reduction: Secure fitment prevents tipping or slipping.
- Operational Efficiency: Optimized paths accelerate order retrieval.
- Worker Safety: Purpose-built access improves handling ergonomics.
- Inventory Visibility: Streamlined configuration supports rapid scanning and stocktaking.
Key Takeaway Summary Table
Issue Faced | Custom Racking Solution | Benefit Gained |
---|---|---|
Irregular Load Shapes | Adjustable cantilever or cradle | Damage prevention, safe handling |
Weight Concentration | Reinforced structural racking | Structural stability |
High Retrieval Frequency | Mobile and modular racking | Faster access, higher throughput |
Layout Constraints | Tailored aisle planning | Improved forklift navigation |
Compliance Requirements | Certified design and installation | Safety and legal assurance |
FAQs
- What materials can be stored in cantilever racks?
Long and bulky goods such as metal beams, pipes, timber, and sheet products are best suited for cantilever racking systems due to their unrestricted horizontal layout. - Are custom racking systems more expensive than standard ones?
Initial costs are higher, but operational savings in damage prevention, efficiency, and safety outweigh the expense over time. - How do I ensure compliance with racking safety regulations?
Engage certified structural engineers and require detailed load certifications. Follow region-specific standards and schedule regular inspections. - Can mobile racks support oversized materials safely?
Yes, with proper rail anchoring, load balancing, and engineered safety stops, mobile systems can support non-standard goods while improving space efficiency. - Do all warehouses benefit from custom racking?
Custom systems are most valuable where materials deviate from standard sizes, or where conventional storage undermines productivity or safety.
Do you need more information?
Our team of experts will be happy to help you with any questions you may have.
More information